With the rapid development of electronic technology , as well as one of the significant trends of modern electronic products are widely used in wireless communication technology in various fields , high-frequency , high-speed , high-density has gradually become . High-frequency signal transmission and high-speed digital technology , forcing the PCB to the tiny hole buried / blind hole of the wire fine, uniform thin dielectric layer , high-frequency high-speed high-density multi-layer PCB design technology has become an important area of research.
High frequency PCB design
High-frequency high-speed high-density multi-layer PCB design techniques
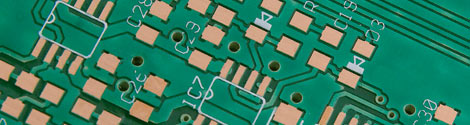
1 . The layout design
Protel although with automatic layout function , but it does not fully meet the operational needs of high frequency circuit designers often by virtue of experience , depending on the circumstances , the first using the method manually adjust some components to optimize the layout of the location , combined with automatic layout the overall design is completed PCB . Reasonable or not directly affect the layout of the life of the product , stability , EMC ( electromagnetic compatibility ) , etc., must be from the overall layout of the circuit board , wiring continuity and PCB can be manufactured , mechanical structure , thermal , EMI ( electromagnetic interference ) , reliability, signal integrity and other aspects to consider.
Usually the first place with the mechanical components related to the size of the fixed position , then place special and larger components , and finally placing small components . Also, the wiring requirements for both the high frequency components to be as compact as possible to place the signal line wiring as short as possible in order to reduce cross-interference signal lines and the like.
1.1 Mechanical dimensions and positioning related to the placement of the plug
Power sockets, switches, interfaces between PCB , lights , etc. are related to the size and positioning of the mechanical plug-in. Typically , the interface between the power supply and PCB placed at the edge of the PCB, and the PCB edge should be 3 mm ~ 5 mm spacing ; indicator LED should be accurately placed according to need ; switch and some fine-tuning components, such as adjustable inductors, variable resistors , etc. should be placed close to the edges of the PCB , and connected to the adjustment ; need for frequent replacement of components must be placed in the position of the device is relatively small , easy to replace .
1.2 Special components placed
Power tubes , transformers, rectifiers and other heating devices , heat generated when working at high frequencies , which is why the layout should be fully considered in the ventilation and cooling, such components will be placed on the PCB where air circulation is easy . Power rectifier tubes should be fitted and adjusted the radiator , and to stay away from the transformer . Electrolytic capacitor elements like heat intolerance should also stay away from heating devices , otherwise it will be dried electrolyte , causing its resistance increases , performance deteriorated , affecting the stability of the circuit.
Failure -prone components , such as adjusting the tube , electrolytic capacitors, relays, etc. , should also be considered when placing the easy maintenance. Often need to test point measurement , taken to ensure that the probe should be able to easily layout components in contact with .
Due to the internal power supply will produce 50 Hz leakage magnetic field , when coupled with certain parts of the cross-linked low-frequency amplifier , the amplifier will produce low-frequency interference . Therefore, they must be isolated or be shielded. Preferably at levels of amplifiers arranged in a line schematic form , the advantages of such a method is ground current discharge levels in the closed current level does not affect other circuits . The input stage and the output stage should be as far away from the interference to reduce the parasitic coupling between them .
Consider the relationship between the signal transmission between the functional circuit of each unit , but also the low-frequency and high-frequency circuit to separate circuits , analog and digital circuits separated. IC should be placed in the center of the PCB , so easy to connect with each pin wiring other devices.
Inductors, transformers and other devices with magnetic coupling , should be placed orthogonal to each other , in order to reduce the magnetic coupling . In addition, they have a strong magnetic field , which should be large in a large space or a magnetic shield to reduce the influence of other circuits .
In the key parts of the PCB to configure the appropriate high-frequency decoupling capacitors , such as PCB power at the input should be connected to a 10μF ~ 100 μF electrolytic capacitor , in the vicinity of IC power pin should be connected to a 0.01 pF porcelain around chip capacitors . Some circuits have to configure the appropriate high or low frequency choke to reduce the impact of high frequency circuits. This is illustrated in the schematic design and drawing when it should be taken into account , otherwise it will also affect the performance of the circuit.
Spacing components to be arranged when appropriate , the spacing should take into account the possibility of breakdown or arcing between them.
Push-pull circuit comprising , a bridge amplifier circuit , when the electrical parameters of components disposed attention symmetry and symmetry structure , so as distributed parameter line symmetrical components .
After the completion of the main components of the manual layout methods should be used to lock components so that these components do not move when the automatic layout. Edit change that execute commands or components selected in the Properties can be locked Locked longer moves .
1.3 Common components placed
For ordinary components, such as resistors, capacitors , etc., should be neatly arranged components , footprint size , several aspects of continuity and can be soldered wiring considerations such as convenience , can be auto- layout mode .
2 . the wiring design :
Wiring is realized on the basis of rational distribution of the overall requirements of the high-frequency PCB design . Including automatic and manual wiring wiring wiring in two ways. Typically , the number of signal lines regardless of how much the key , the first of these signal lines for manual wiring , the wiring is completed on these signal lines wiring carefully examined , after checking through its fixed , and then the other wiring for automatic routing. Which uses a combination of manual and automatic routing to complete the PCB layout .
Should pay particular attention to the following aspects in the wiring process in high frequency PCB .
2.1 wiring to :
Wiring circuits in accordance with the best signal flow using the whole line , available when needed turning 45 ° polyline or arc curve to complete, thus reducing the coupling of external high-frequency signal transmission and each other. High-frequency signal wiring lines as short as possible . According to the operating frequency of the circuit, a reasonable length of the selection signal line wiring , thus reducing the distribution parameter , reducing signal loss . When making double-sided , two levels on adjacent wires perpendicular to each other the best , oblique or curved intersection . Avoiding parallel to each other , thus reducing the mutual interference and parasitic coupling.
High-frequency and low-frequency signal line signal line should be separated as much as possible , take the shield when necessary measures to prevent mutual interference. For a relatively weak received signal input terminal , the external signal is susceptible to interference , the shield can be made using ground or surrounded by the high frequency connector good shielding. On the same level, parallel lines should be avoided , otherwise it will introduce distribution parameters , have an impact on the circuit . May introduce a grounded copper foil between two parallel lines if not avoided, constitute the line of separation .
In digital circuits , the differential signal lines , the line should go in pairs , try to make them parallel , close to some , and the length or less .
Form 2.2 wiring
PCB routing process , the minimum width of the traces is determined by the adhesion strength between the conductor and the insulating layer substrate, and the current intensity flowing through the conductor . When the foil thickness is 0.05mm, a width of 1mm ~ 1.5 mm, through the current of 2A . Temperature no higher than 3 ℃, except for some special alignment , the other on the same level wiring width should be as uniform as possible . In the high frequency circuit wiring pitch will affect the size of the distributed capacitance and inductance , thus affecting the stability of the signal loss caused by the interference signal and the circuit or the like . In the high speed switching circuit , the pitch of the wire and the transmission time will affect the quality of the signal waveform . Therefore, the minimum wiring pitch to be greater than or equal 0.5 mm, as long as allowed , PCB preferably relatively wide wiring lines .
Printed wire and PCB edge should leave some distance ( not less than the thickness ) , which not only easy to install and machining , but also improve the insulation performance .
Only when encountered in wiring to connect a large circle around the line , to take advantage of the fly line , which is connected directly with the short-term to reduce interference caused by long-distance traces .
Circuit containing magnetic elements which are more sensitive to the surrounding magnetic field, and high-frequency circuit wiring work easily bend electromagnetic radiation , if placed in a magnetic element PCB should ensure that their wiring around the corner there is a certain distance.
Wiring on the same level does not allow cross . Who may cross the line , can be "boring " and "around" a solution that allows a lead from the gap at the other resistors, capacitors , transistors and other devices pin down the "drill " in the past , or from a possible cross section One end of the lead "around" in the past. In particular, if the circuit is very complex, in order to simplify the design , but also allows the cross wire jumper solve the problem .
When a high frequency circuits operating frequency, but also need to consider the effect of impedance matching and antenna wiring problem .
2.3 power lines and ground wiring requirements
Depending on the size of the different operating current , try to increase the width of the power cord . PCB high frequency should be used and a large area of the ground at the edge of the PCB layout , signal interference can reduce the external circuit ; while grounding wire to make PCB good contact with the housing , so that the PCB is closer to the ground voltage earth voltage. Grounding should be selected depending on the circumstances , different low-frequency circuit , the ground wire should be used near high-frequency circuit or grounding manner ground , ground short and thick as possible to reduce the ground impedance , which allows current required to achieve 3 times the standard operating current. Speaker wire should be connected to the PCB ground the amplifier output stage ground , not arbitrary ground .
It should also be timely to lock in some reasonable wiring routing process , in order to avoid repeated wiring . That command execution EditselectNet select Locked in the pre- wiring properties can no longer be locked to move .
3 . the design of the pad and the copper
3.1 pad with aperture
In ensuring the wiring does not violate the minimum spacing distance between the electrical design , the design of the pad should be large enough to ensure that the ring width . The hole than the general components pad diameter slightly larger lead , design is too large, easy to form Weld in welding . Usually the pad is not less than the outer diameter D (d +1.2) mm, where d is the inner pad size , density is relatively large for some of the PCB, may be taken as the minimum pad (d +1.0) mm. The pad is usually provided as a circular shape , but the pads of the integrated circuit package DIP preferably racetrack-shaped , so that the area of the pad can be increased in a limited space , the integrated circuit is conducive to welding. Connection wiring should be a smooth transition with the pad , that is, when the wiring into the circle pad width than the diameter of the circle pad hours, should make teardrop design .
Note that the size of the internal diameter d of the pad is different, should be considered , such as component holes and mounting holes , etc. according to the actual size of the slot the diameter of the lead part . The pad pitch should be considered according to the actual installation components , such as resistors, diodes, capacitors and other tubular element of " vertical ", " horizontal " two installation methods , these two methods are pitch different. Further , the pad pitch of the design should also consider the requirements of a minimum gap between the components , particularly the gap between the specific components from the pitch between pads need to be guaranteed.
In the high-frequency PCB , and also to minimize the number of vias , which can reduce the distributed capacitance , but also increase the mechanical strength of the PCB. In short, high-frequency PCB design, pad and shape , diameter and pitch of the design is necessary to consider its uniqueness , but also to meet the requirements of the production process . Using a standardized design , can reduce product costs, but also improve production efficiency at the same time ensuring product quality .
3.2 copper
The main purpose is to improve the copper anti-jamming capability of the circuit, while the intensity of the heat PCB and PCB great benefit , shielded copper grounding can play the role . Large area but not a strip of copper foil as used in the PCB will be greater when the heat is too long , then strip off the copper foil and easily swell and, therefore , preferably used when the copper grid like copper and circuit ground network connectivity with this grid , so the grid will have better shielding effect , the size of the grid network to focus on shielding interference frequency.
After completing the wiring , pads and vias should be designed to perform DRC ( design rule check ) . Details the differences between the rules defined by the design of the plan between the test results , you can find out the network does not meet the requirements. But first, before wiring the DRC should set parameters before running DRC, namely the implementation of ToolsDesign Rule Check command.
4 . Conclusion
PCB high-frequency circuit design is a complex process , involving many factors are likely to be directly related to the highfrequency circuit performance . Thus , designers need to continue to study the actual work and explore and experience, combined with the new EDA ( Electronic Design Automation ) technology to design a good performance of high frequency circuit PCB.
Contact way
Shenzhen JieTeng Precision Electronics Co., Ltd.
Contact Person: Sophia Wen
Mobile:13510797526
Q Q: 3342625352
Phone:0755-23500787
Fax : 0755-27099486
Skype : JTPCB ; JIETENGPCB
|
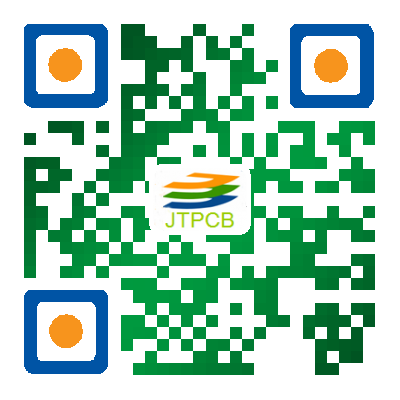 |
Article keywords:High-Frequency Circuit Design and PCB Layout Experience